How Are Sunglasses Made
Understanding how are sunglasses made needs learning of the different parts of glasses, materials, and making glasses processes involved. For example, making eyeglasses is a complex process. Even though there are no fancy electronics, the over 200 handmade steps need very careful teamwork. Also, the quality stand on size is extremely strict, with allowed differences as small as a hair.
We all know we should cherish the fruits of our labor. Therefore, when you gain a deeper understanding of how glasses are manufactured, you will come to enjoy your own sunglasses even more. Moreover, when you start your own sunglasses brand and work with manufacturers, you will be better to design and produce sunglasses that cater to the likes and needs of your target market.
It’s important to note that quality is most important when making sunglasses, and we must meet strict standards such as CE, ISO 12870, ISO 12312-1, ANSI Z80.3 ,ISO and ANSI Z80. Working with reputable sunglasses manufacturers ensures that your sunglasses are of high quality and meet these standards.
Table of Contents
1. How are sunglasses made step by step
Let us discuss making sunglasses in depth together.
1.1 Everything you need to know before how to make sunglasses
1.1.1 How to Designing Sunglasses
1.1.2 What Are the Different Parts of Sunglasses
1.1.3 What Are Glasses Made Of
1.1.4 Sunglasses Manufacturability review: one of the key step glasses making
- Also known as pre-production evaluation is a process analysis that improves product quality and manufacturability. It assesses the design, performance, and technical level of the enterprise to suggest improvements. Its goal is to enhance product quality and efficiency, adapt the design to production conditions, and increase economic benefits.
- Excellent eyeglass product structure and manufacturing process can improve eyewear quality and ensure high-quality stability, ensure glasses product durability and reliability, It can be seen that the structural process analysis and review of glasses is an important content of process preparation.
1.1.5 Contents of Manufacturability Review of Sunglasses Product Structure
1. Is the angle of the eye rim grooves reasonable? ( 90 ,100 ,105,110 degrees )
2. Are the lenses easy to pop out? (eye rim grooves shape : V , U , 凸 , 凹 )
3. What material to choose for the eye rim to be hard enough ?
1) According to the material: (nickel copper, special material, copper skin, stainless steel, titanium, acetate, TR90)
2) The cross-sectional area of different materials can be used to calculate the width and thickness of various materials that can pass the test
3) The minimum R standard of different material loops that can be winding (the eye-shaped edge R cannot be less than **R)
4. Whether there are supporting rim lock (rimlocks include: cashew rimlock, flat rimlock, vertical rimlocks, Sub-Rimlock)
1) Rimlock shape data
2) Rimlock type (with round backing rim, formula backing rim)
5. Is there a winding tool and supporting tools
6. Is there a tool for cutting lenses
7. Is there a matching nylon line for the semi rimless?
8. The shapes of different Rim need to specify different surface treatment methods to protect the shape of the Rim, such as patterns, and the polishing method and drum time must be specified
1. Whether the thickness of the front sheet is strong enough (top view)
1) Soldering rim with sheet frame (0.8–1.4MM) cupronickel, titanium sheet, special sheet, stainless steel sheet, skin copper sheet, B titanium
2) Carved eye rim grooves frame (1.6-2.0MM above white copper, titanium sheet, special sheet, skin copper sheet, B titanium sheet)
3) The frame that clamps the lens (0.5-0.6MM, stainless steel sheet, B titanium sheet)
2. Whether the minimum width of the rim edge meets the processing pole root (front view)
3. What material should be used to be hard enough and not soft?
4. Whether the selected material needs heat treatment
5. Whether there is a position beyond the processing limit
6. The eye rim groove shapes (convex bone/square pit/V pit/U pit/whether there are special requirements for groove)
7. Does the front sheet need stamping (pattern, surface, groove, refer to the stamping processing limit)
8. Whether it is necessary to do double color, the double color position needs to be obvious (see the processing standard of the double color position boundary line for details)
9. Consider the number of soldering points (more soldering points will increase the cost)
10. Consider whether cutting is required
11. Consider whether it is necessary to reserve a processing allowance (drum/gong cutting/cutting after reserved beer bending)
12. Is the bridge of the front sheet strong enough?
13. The processing method of the front sheet (laser cutting/stamping cutting)
14. Whether the front sheet is a combination of metal and acetate
1. Is the overall size of the bridge the standard size of our factory?
2. What material is required for standard dimensions to ensure strength?
1) Special wire (2.3MM*1.8MM*2.3MM thickness when viewed from above, not less than 1.5MM when viewed directly)
2) Stainless steel wire, beryllium copper wire, cupronickel wire, pure titanium, B titanium must strictly comply with the standards of our factory
3. Bridge processing method (laser cutting/hydraulic flashing/casting)
4. How to cut the bridge with eyerim (ordinary gong cutting/carved gong cutting)
5. Whether the bridge is double-colored (0.3MM high and low positions are required, refer to the stamping processing limit)
6. Whether hardening treatment is required
7. Soldering method of bridge matching Eyerim (edge soldering/gong-level soldering)
1) The material of the bridge and the eye rim cannot be the same stainless steel (easy to desolder)
2) Pay attention to the hardness of the eye rim when soldering the bridge (special wire is not recommended)
3) Soldering on the edge of the rim, it is necessary to ensure that the level margin of the gong bridge should not be less than 0.5MM
8. Whether the size of the soldering position will affect it (the soldering position is not strong/the edge of the soldering position is deformed by force)
1) If the soldering position is too small, it is easy to cause weak soldering points and desoldering
2) The soldering position is small and easy to deform the edge of the eyerim
1. Whether the external dimensions conform to the minimum processing limit standard of our factory (see the processing limit of stamping of eyeglass parts)
2. What material to choose to ensure strength
1) Cupronickel material (stamping: width 3MM*thickness 1.3MM or more, without stamping: width 3.5MM*thickness 1.4MM or more)
2) Skin copper material (width 1.8MM*1.2MM or more)
3) Stainless steel (width 1.8MM*1.2MM or more)
4) It is not recommended to use special wires for end pieces
3. End pieces processing method (laser cutting/stamping/casting/cutting)
4. The method of gong cutting that matching the eye rim (ordinary gong cutting/finely carved gong cutting)
5. Whether the end piece needs to be hardened
6. Cooperate with the soldering method of the eye rim (edge soldering/gong level soldering)
1) Refer to the soldering method of the bridge with the eye rim
7. Whether there is a diamond hole in the bend of the end piece (see the diamond processing guide for the bend of the end piece for details)
8. Does the end piece need to match the rubber or acetate temple?
9. The thickness of the matching acetate temple of the end piece and whether there is a matching high and low hinge for the matching acetate Try to choose a hinge that is suitable for the height
10. Whether the end piece is with bent and stamping out together, pay attention to increase the gong cutting margin
11. Whether it is connected with the Sub-Rimlock, and whether the rimlocks have matching stock parts
12. Is the size of the end piece enough for the limit of the size of the rimlock?
13. Whether there are more or less soldering points on the inner side of the end piece, and whether sandblasting is required
14. Whether it is necessary to match the end piece of the acetate, the eyebrow, and consider the processing method (coordination method)
15. Whether there is a dead angle of spraying color and color defects that are easy to fall off, pay attention to notify the customer in advance
16. Does the bending affect the pattern? There should be no deep or high pits or patterns at the bending place
17. Consider installing diamonds (diamond flat/low point) for details, please refer to diamond assembly and processing standards
18. Consider the thickness of the diamond end piece
19. Considering the length of the end piece is sufficient for the length of the soldering hinge and the size of the rim lock used, pay attention to selecting a suitable hinge
20. Whether the hinge soldering is centered or eccentric
1) The temple of the double-hinge model must be parallel to the center of the two hinges of the end piece
2) Pay attention to the shape of the acetate temple. If it is a side-cut style, the position of the soldering hinge must be determined
21. Is it necessary to reserve a machining allowance for the incision of the end piece and the position of the eye rim?
22. Whether the surface is too large, pay attention the polishing
1. Whether the material used can ensure the strength
2. Processing method (corrosion/oil pressure/laser cutting/stamping cutting/casting)
3. Whether there are concave characters on the temple, and the depth of the concave characters (see the processing limit of the upper concave characters for details)
4. Is there a high and low level at the bottom of the temple
5. Pay attention to the width of the temple and select the hinge size
6. Consider the polishing and coloring data of the temple of large area width (note the processing limit, it cannot be gold and silver)
7. Consider whether the temple of large area width has stamping concave and convex characters
8. Consider whether a special measuring tool is required for the temple and the fitting end piece
9. Does the pattern on the temple affect the strength of the temple?
10. Consider the color/sand blasting/wrapping paper/diamond process of temple
11. Consider the thickness of soldering spot / processing difficulty < cost / quotation >
1. Cutting method (knife die cutting/fine carving cutting)
2. Whether it needs fine carving, whether the leather is thick enough
3. Whether it is a standard material (standard material is 3.5MM, 4.0MM, 6.0MM)
4. Is it necessary to laminating, the thickness and strength of the materials, and whether it is necessary to leave a processing position
5. Whether it is a transparent material
6. Is there a supporting hinge for the cooperation between the temple and the end piece?
7. Does the Core wire need to be eccentric?
8. Whether the processing limit is exceeded (see core wire processing limit standard for details)
9. The surface of the core wire is (shiny finished / pattern / sandblasting)
10. Does the acetate temple need to be assembled with stamping trim or logo?
11. The color of the core wire of the acetate temple (the gun color is easy to fade, and the copper core is easy to break)
12. Consider the strength of the acetate temple
1. What tests are required (spectacle shuttle test/optical test)
2. Nose Pad Selection
3. The strength of the whole frame, and whether a flex hinge is required
4. Whether the strength of the whole frame is reasonable
5. Whether there is a hidden danger of accessories falling off in the glasses frame of children’s wear, and whether there is a hidden danger to people
6. Whether there is a matching position that is easy to fall off the color
7. Is there a ready-made stop hinge for the whole frame, and whether it needs to be drawn
8. Consider if temple hit the lens
1.1.6 Making Sunglasses Frames Prototype
- Inspect appearance and structure: Using processes such as 3D rapid prototyping and CNC machining, create a realistic appearance or functional prototype to allow customers, designers, and engineers to evaluate and optimize the shape and structure.
- Predict the problems that may occur in the mold and manufacturing process: Through prototype production, possible problems in mold production and other production processes can be found, and problems such as mold modification and reordering of materials can be avoided, thereby reducing production costs and risks.
1.2. How to Make Metal and Acetate Glasses
How to make sunglasses? This is a complicated process that requires the close cooperation of all our staff to produce eye glasses step by step, such as strict glasses quality standards, guidelines for the making process of eyewear, and a complete feedback and improvement mechanism for all problems in the sun glasses production process.
1.2.1 How Are Glasses Metal Parts Made
Custom metal parts(end pieces/temples)production
(1) Making Drawings and Program the CNC machine
First, a design drawing of the customized metal part is needed, including dimensions, shape, and functionality. Computer-aided design (CAD) software is typically used to create an accurate digital model.
(2) Making Stamping die creation
Based on the design drawing, a stamping die is made. The die-making process includes selecting die materials, die machining (such as CNC machining, electrical discharge machining), and die assembly.
(3) Material selection
Select a metal or metal alloy suitable for producing the customized metal part. Considerations include durability, weight, corrosion resistance, and possible allergies or sensitivities. Common metal materials include stainless steel, titanium, aluminum, phosphor bronze, and Monel.
(4) Stamping process
Place the metal sheet into the stamping die and apply pressure using a stamping press, shaping the metal material. Stamping can achieve complex part shapes and precise dimensions. Stamping processes include various methods such as blanking, punching, bending, and deep drawing.
(5) Swaging process
Place the metal bar or tube into the swaging die, and apply pressure using swaging equipment, causing the metal material to change shape. Swaging can achieve precise dimensions and shapes, including methods such as rotary swaging, axial swaging, etc.
(6) Making Trimming
(7) Vibratory Tumbling Parts
(8) Polishing Parts Of Glasses
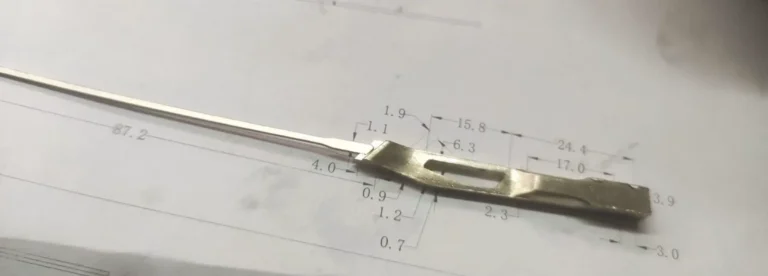
(9) Quality inspection
1.2.2 How Are Metal Frames Made
(1) The production of eyeglass eye rims
he main component of eyeglasses is the frame, which is made. up of rims formed by winding. They are usually produced using automated winding machines.
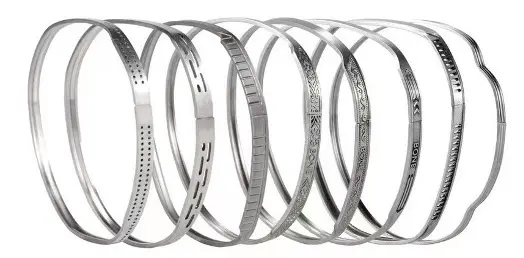
According to the engineering technical drawings 1:1 ready to make,The fully automatic winding machine is a high-tech product that integrates precision machinery, electronic technology, and computer technology. It can automatically scan lenses and templates, and the operation is simple.
The graphic output system is compatible with various file formats of drawing software, enabling the production of materials such as pure titanium rims, alloy titanium rims, stainless steel rims, high nickel alloy rims, Monel rims, and phosphor bronze wires, with stable results.
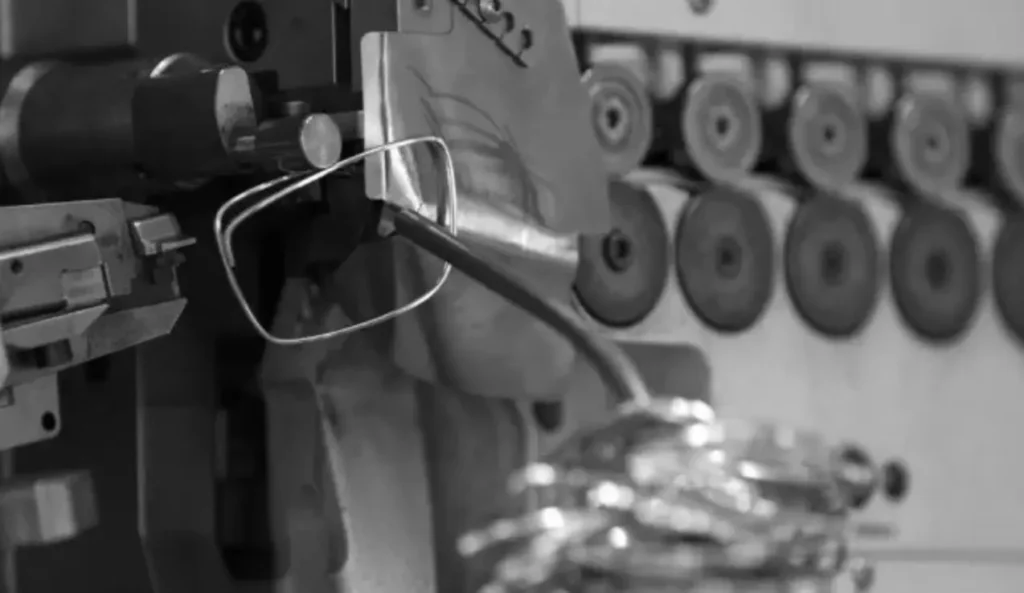
(2) Soldering :an important process in glasses production
All parts of eye glasses are joined together using soldering machines. Soldering is a unique process in the sunglasses production of metal eyeglasses, and the quality of soldering techniques and solder points directly affects the quality and grade of making metal eyeglass frames.
Depending on the different positions and styles of eyewear, the process requirements and technical indicators also vary. During all soldering processes, it is essential to ensure that the parts of glasses are clean and bright, have stable fixtures, control soldering power, and control the location and range of soldering.
Undesirable phenomena such as de-soldering, insufficient soldering, solder accumulation, discolored solder joints, and soldering damage that are detrimental to the soldering strength must be absolutely avoided.
(2.1) Soldering the rim lock
Soldering the rim lock is the first step in making eyeglass frames. The quality of the rim lock soldering directly affects whether the frame’s appearance is symmetrical, aesthetically pleasing, and sturdy.
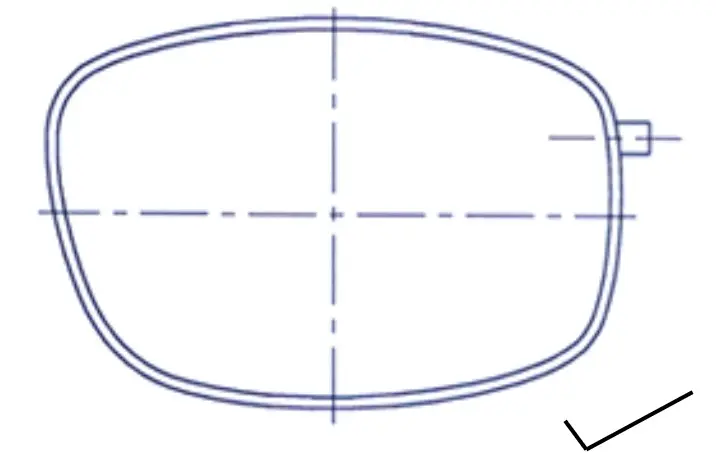
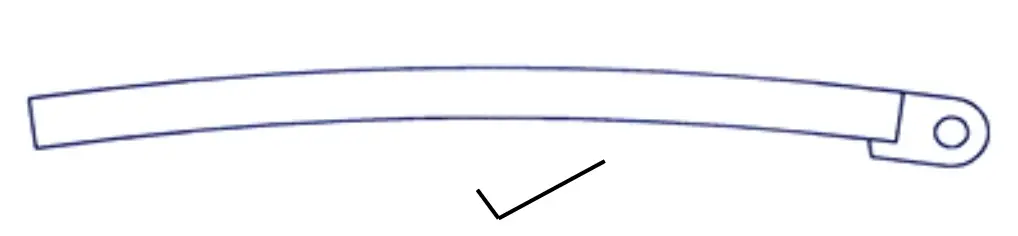
(2.2) Soldering the bridge
The soldering bridge of making glasses is the most important step in the process of how to make glasses.
The bridge is the central part of the frame that connects the eyewires and rests on the wearer’s nose. Soldering is used to join the bridge to the eyewires or rims. The components are aligned, and solder is applied to the joint to create a strong connection.
(2.3) V-cutting the rim lock
The V-cut is a notching process that creates a recess in the rim lock to accommodate the lens securely. After the V-cut is made, the lens is inserted, and the rim lock is tightened to hold the lens in place.
It seems to be a simple glasses manufacturing process, but it is very critical. The lenses need to be replaced frequently, and the clamp screws need to be loosened and tightened. The durability is very important to the eyewear manufacturing and quality of glasses.

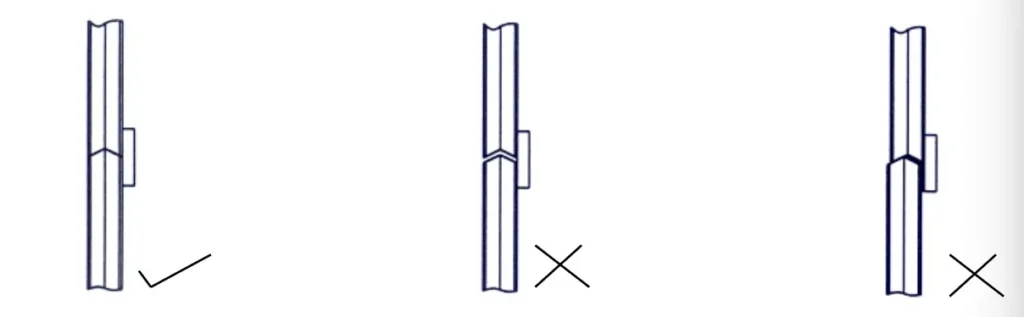
(2.4) Soldering the pad arm
The pad arm is a component that holds the nose pads and attaches to the bridge or eyewire. Soldering is used to join the pad arm to the front fo frame. Pay attention to distinguishing between the left and right sides, and ensure that they are symmetrical, have consistent heights, and match the engineering technical drawings.It is also an important step in the glasses production process.
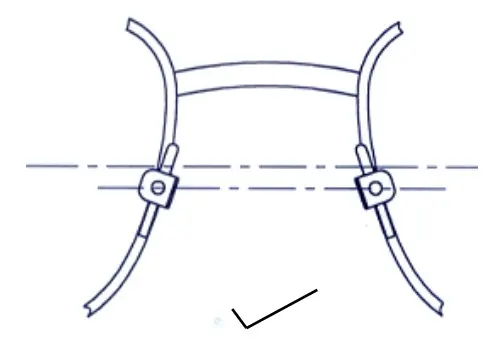
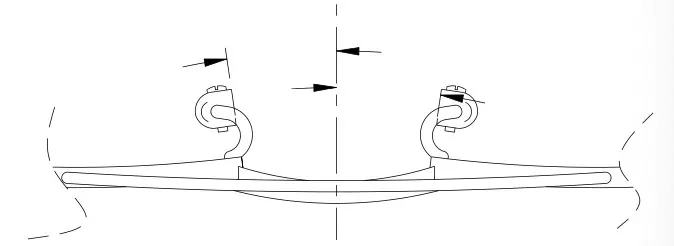
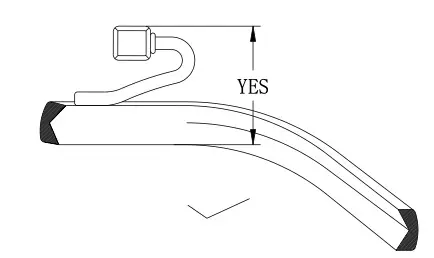
(2.5) Soldering the end pieces
The end pieces are the parts of the glasses frame that connect the temples to the frame front. Soldering is used to join the end pieces to the frame front and temples. Soldering the end pieces is usually the final step in the sordering process, and its technical difficulty is relatively the greatest in the sunglasses production. It’s challenging to master, so it’s essential to pay attention to the skills and proficiency in operation.
(2.6) Soldering Quality inspection
The focus is on the soldering strength and appearance. It is essential to check against the engineering technical drawings.
(3) Glasses Production :Polishing
The process can be categorized into three main stages – accessory polishing, semi-frame polishing, and full-frame polishing. Polishing is a critical process in eyeglass production and requires a high level of precision. This procedure directly impacts the surface quality, determines the level of the frames, and contributes to the overall appearance of the eyeglasses.
To ensure the highest quality, it is crucial to eliminate any scratches, marks, or defects during the polishing stages in sunglasses production. Additionally, a 100% inspection should be conducted after the full-frame polishing to guarantee that every pair of eyeglasses meets the required quality standards before proceeding to the next step, such as lens fitting or final quality control checks. This thorough approach ensures the production of high-quality, comfortable, and visually appealing eyeglasses.
(3.1) Parts polishing
This stage involves refining individual frame parts, such as the bridge, end pieces, and temples. The process removes any irregularities, burrs, or sharp edges, ensuring a smooth and comfortable fit for the wearer.
(3.2) Semi-frame polishing
After Soldering the pad arm, the semi-frame polishing focuses on the position of soldering and dead-end positions ensuring that joints and connections are smooth and flush. This stage also helps to refine the overall shape of the eyeglass frame in sunglasses production.
(3.3) Full-frame polishing
Once the eyeglass frame is completely assembled, the full-frame polishing process enhances the frame’s surface finish. This step in sunglasses production involves using various polishing compounds and tools to achieve a smooth, even, and shiny surface, highlighting the frame’s design and quality.
(4) Glasses Production : Barrel Tumbling
Tumbling is a cost-effective and efficient mass finishing sunglasses production process that can handle large quantities of eyeglass frame components simultaneously. Maximize the uniformity of the eyeglass frame’s brightness and the delicacy of its gloss. A better surface condition is essential to ensuring the adhesion and smoothness of subsequent electroplating processes.
This process is relatively mysterious. Friends often ask which step is this process in how to make glasses?
(5) Glasses Production : Plating and Color Coatting
Plating and color coating are two distinct finishing processes used in the eyeglass industry to enhance the appearance, durability, and corrosion resistance of eyeglass frames.It is most important in sunglasses production. Also friends often ask how to ensure quality and environmental protection in the process of how to make glasses.
Plating: This process involves applying a thin layer of metal, such as gold, silver, or nickel, onto the surface of the eyeglass frame using electrochemical methods. The frame is submerged in a plating solution containing metal ions, and an electric current is applied to deposit the metal ions onto the frame’s surface, forming a protective and decorative coating. Plating can provide a variety of finishes, from shiny to matte, and improves the frame’s resistance to wear and corrosion.
Eyeglass frame plating can be done only after the completion of the color treatment, the way to add color basically spray color baking dry process, but to ensure the adhesion of the spray color, then you must first carry out the curing agent priming process.The adhesion is very important in making sunglasses.
After the ordinary metal frame is done in color, the last need to do glue processing, usually using the electroplating Lak frame oil (closed paint); sprayed on the surface of the eyeglass frame, the plating surface has excellent protection, good hardness, strong adhesion, alcohol and salt spray chemical resistance, is the protective paint. There are two kinds of effects of adding glue: light glue and matte glue.
(6) Glasses Production : Packaging
Glasses packaging is the last process of glasses manufacturing before the finished product leaves the factory. The quality of packaging is the most intuitive feeling of consumers on products and directly affects the sales of products.so it is important in making sunglasses.
(6.1) Cut Lens
Cutting demo lenses and sun lenses is a crucial step in the manufacturing sunglasses and assembly process for eyeglasses and sunglasses. Demo lenses are non-prescription lenses used in eyeglass frames displayed in stores, while sun lenses are tinted lenses used in sunglasses to protect the eyes from.
Cutting demo lenses and sun lenses accurately ensures a professional appearance and a comfortable, secure fit for the wearer. Properly cut sun lenses also provide optimal UV protection and glare reduction, enhancing the overall visual experience for the wearer.
(6.2) Printing
Printing brand details, size, and color information on eyeglasses or sunglasses is an essential aspect of branding and product identification. These details are typically printed on the inside of the temples or on the lens itself. Here are some methods for printing this information:
Pad printing is a popular method for transferring two-dimensional images onto three-dimensional objects, such as eyeglass frames. A silicone pad is used to pick up ink from an etched plate and transfer it onto the frame’s surface. This technique is suitable for printing on a variety of materials, including metal and plastic, and allows for precise, detailed prints.
Laser engraving uses a laser beam to etch the brand details, size, and color information directly onto the surface of the eyeglass frame or lens. This method provides a permanent, high-quality marking that is resistant to wear and tear.
Digital printing for sunglasses production or unique designs, digital printing can be used to transfer images directly onto the surface of eyeglass frames or lenses. At present, it is a popular process in making sunglasses.
When printing brand details, size, and color information, it is essential to choose the appropriate method based on the material of the eyewear and the desired level of durability. Properly printed information not only contributes to the branding and product identification but also helps customers and opticians identify the product’s specifications and ensure a proper fit for the wearer.
(6.3) Bending Acetate End-tip
Bending the acetate end tips of eyeglass temples is necessary to provide a comfortable and customized fit for the wearer.
(6.4) Assembly lenses and nose pads
Assembly lenses and nose pads on eyeglass frames is essential for ensuring proper vision correction and a comfortable fit for the wearer.
(6.5) Adjustment eyeglasses frames
Adjusting eyeglass frames is an essential step in sunglasses production to ensure a comfortable and secure fit for the wearer. Properly adjusted frames can effectively reduce discomfort, prevent slippage, and improve the overall visual experience.
- Frame alignment: Ensure the front of the frame remains balanced on a horizontal plane.
- Bridge alignment: The bridge should fit snugly on the nose, providing stable support.
- Nose pad alignment: Nose pads should fit snugly on both sides of the nose, distributing weight evenly.
- Temple alignment: The tail of the temples should fit snugly against the head, ensuring comfort and stability.
- Stability when placed upright: Glasses should remain stable when placed upright.
- Stability when placed upside down: Glasses should remain stable when placed upside down.
- Symmetrical opening: Temples should remain symmetrical when opening and closing.
- Symmetrical end pieces: The end pieces on both sides of the frame should match the wearer’s facial contours.
- Symmetrical tilt angle: The pantoscopic angle of the temples should be consistent on both sides.
Properly adjusting eyeglass frames in sunglasses production helps ensure wearer comfort and optimal vision correction. During the adjustment process, follow the above requirements to achieve the best results.
(7) Sunglasses Production : Quality control of finished glasses
The sunglasses production process of metal eyeglass frames involves multiple steps, and both semi-finished and eyeglasses finished products undergo strict quality inspections. Quality control is particularly stringent after the polishing step, with a strong emphasis on examining and testing the structural, dimensional, and surface conditions during the eyewear manufacturing process.Strictly abide by the ISO testing standards.
(8) Sunglasses Production : Cleaning and packaging
Cleaning and packaging are essential steps in the sunglasses production process of eyeglasses to ensure that the final product is hygienic, well-presented, and protected during shipping and handling.
1.2.3 How Are Acetate Frames Made
Before glasses production, the production order, drawings, and customer-confirmed samples must be carefully and rigorously checked. All requirements must be combined with these eyeglasses production order to confirm production process.
(1) Sunglasses Production : Raw Material Cutting / Sawing sheet: Front and Temple
- Sawing sheet is an important step in the eyeglass frame manufacturing process, especially for acetate frames. In this step, the acetate sheets are cut into blocks of the required length and shape, taking into consideration factors such as material distribution, texture, and color.
- By carefully planning and executing the sawing sheet process, manufacturers can create high-quality acetate eyeglass frames while optimizing material usage and minimizing waste. This attention to detail can contribute to a more sustainable and cost-effective production process.
(2) Sunglasses Production : Drying acetate
Different colors require different temperatures and times, with the purpose of enhancing hardness and preventing eyeglass frames from deforming.
(3) Making acetate temple
(3.1) Cutting the temple shape / Temple passing
The direction of the cutting temple shape is determined according to the distribution of the sunglasses production materials and the color of the acetate material. Different colors have different cutting temple shape directions to improve the utilization rate of materials
(3.2) Hinge position milling
This approach is more beneficial for the quality of the hinge position when inserting core-wire, resulting in a more visually appealing appearance and improved guidance for the direction of the core-wire.
(3.3) Core wire shooting
Core shooting is to drive core-wire into the interior of the acetate temples. Its function is equivalent to forming the internal support of the temples, and it is the main sunglasses production process of forming acetate temples. After the core-wire are injected into the temples of the glasses, it is as if the heart is injected into the temples, and the temples of the glasses have strength and soul.
Note that different colors of acetate have different temperatures and making sunglasses processes, and ensure that the core-wire is driven into the correct position.
(3.4) Temple milling
According to engineering technical drawings, the milling machine uses a rotating cutting tool to remove. material and create the desired shape and profile of the eyeglass temple. This process allows for precise and accurate shaping, ensuring a comfortable and secure fit for the wearer.
(3.5) Hand skiving shape
Hand skiving the shape of the temple refers to the process of manually sculpting and shaping the eyeglass temples using hand tools, such as knives, files, or sandpaper. This technique allows for a high level of craftsmanship and attention to detail, ensuring a comfortable fit and an aesthetically pleasing appearance.
(3.6) Hinge plastic coating
Coatting the hinge , which will form a protective layer after curing to prevent damage to the hinge when polishing and tumbling.
(3.7) Polishing(edge & temple)
Mainly to deal with the surface roughness after hand skiving, In order to better prepare for the tumbling process.
(3.8) Temple tip curling
Why is it important to curling the temple before placing it into the tumbling ? The reason is that the relatively high-speed tumbling barrel produces heat during operation, which can cause the acetate to heat up and slightly deform. Curling the temple prior to tumbling serves to enhance surface quality and prevent surface wrinkling or damage from occurring during subsequent bending processes.
(3.9) Tumbling the acetate temple
Uses abrasive media and motion to smooth and polish the surfaces. This process helps to remove any rough edges or imperfections, improving the overall surface quality and appearance of the eyeglass temples. Tumbling is an essential step in eyeglass frame manufacturing, ensuring a comfortable fit and a visually pleasing product.Required process rough tumbling, second tumbling and finish tumbling.
(3.10) Polishing the acetate temple
Polishing the acetate temple refers to the process of. Refining and smoothing the surfaces of the acetate eyeglass temples to achieve a high-quality,glossy finish.Polishing is a crucial step in eyeglass frame manufacturing, as it ensures a comfortable fit and an aesthetically pleasing appearance.
(3.11) Temple milling and temple & frame screwing
Cut the temple head according to the finished front of frame: adjust the Opening Angle and Pantoscopic Angle to ensure a perfect fit after assembling the acetate temple with front.
(4) Sunglasses Production : making acetate front of sunglasses
(4.1) Bending bridge
The curvature must be determined according to engineering. technical drawings to ensure symmetry and centering. Check for any crush marks or instances of bridge breakage.
(4.2) Automatic laminating noes pad
Based on the requirements of the technical drawings and production orders, place the cut small pieces of material on the acetate sheet. After Laminating, allow at least 12 hours to pass before continuing to ensure that the bonded areas are firmly attached, preventing cracks or fractures in the final product.
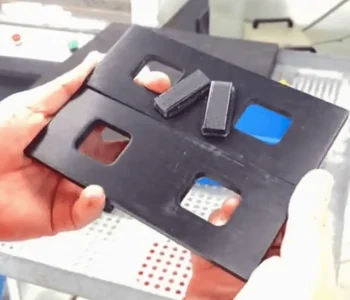
(4.3) CNC cutting front
Pre-adjust the program of the CNC machine, put the material into the material area of the machine, and then follow the program. In this process, in addition to checking the data, the experience of the technician is very important. The data of those places must be 1:1, and the data of some places must be reserved. Only in this way can the final finished product fully conform to the CAD drawing.
(4.4) Hand skiving front
Hand skiving the shape of the front refers to the process of manually sculpting and shaping the eyeglass front using hand tools, such as knives, files, or sandpaper. This technique allows for a high level of craftsmanship and attention to detail, ensuring a comfortable fit and an aesthetically pleasing appearance.
(4.5) Polishing(edge & front)
Mainly to deal with the surface roughness after hand skiving, In order to better prepare for the tumbling process.
(4.6) Tumbling the acetate front
Uses abrasive media and motion to smooth and polish the surfaces. This process helps to remove any rough edges or imperfections, improving the overall surface quality and appearance of the front. Tumbling is an essential step in eyeglass frame manufacturing, ensuring a comfortable fit and a visually pleasing product.Required process rough tumbling, second tumbling and finish tumbling.
(4.7) Rim's bending
Rim’s bending refers to the process of shaping the eyeglass frame’s rim to achieve the desired curvature and fit. This step is essential in eyeglass frame manufacturing to ensure that the lenses can be securely mounted within the frame and that the eyeglasses fit comfortably on the wearer’s face. The bending process can be done using specialized tools and equipment, applying heat if necessary to make the material more pliable and easier to shape.
(4.8) Hinge insertion
The hinge insertion process involves creating precise slots in the front of glasses, then inserting the hinges and fastening them securely by heating. This step is crucial in eyeglass frame manufacturing, as it ensures the glasses’ functionality and durability.
(4.9) Trim milling of the front
Trim milling the front head according to the finished temple: adjust the Opening Angle and Pantoscopic Angle to ensure a perfect fit after assembling the acetate temple with front.
(4.10)Product assembly
Assemble the temple and the front carefully with screws, paying attention to the coordination of the connection positions
(4.11) Polishing frames
Polishing the frames refers to the process of refining and smoothing the surfaces of the acetate eyeglass to achieve a high-quality, glossy finish.Polishing is a crucial step in eyeglass frame manufacturing, as it ensures a comfortable fit and an aesthetically pleasing appearance.
(4.12) Packaging
The packaging process of sunglasses production for metal glasses and acetate glasses may have some differences due to the materials used and the specific requirements for handling and protecting each type of frame. Here are some examples of differences in the packaging process:
(4.12.1)Print: Both metal and acetate glasses may have brand logos or other information printed on the frame or temples. However, the printing techniques and materials used may vary depending on the frame material. For metal frames, techniques like laser engraving and pad print might be more common, while for acetate frames, pad printing or hot foil stamping could be more suitable.
(4.12.2)Adjust: Before packaging, both types of glasses need to be adjusted to ensure a proper fit for the wearer. Metal frames are usually more malleable and can be easily adjusted with pliers. In contrast, acetate frames may require heating to make them more pliable before adjustments, especially when reshaping the temples or adjusting the curvature.
(4.12.3)Clean: Cleaning methods for both metal and acetate glasses are generally similar, involving the use of a soft cloth and a gentle cleaning solution to remove any fingerprints, dust, or debris. However, acetate frames may require extra care to avoid damaging the finish, while metal frames may need additional attention to prevent potential corrosion or tarnish.
Overall, the packaging process for metal and acetate glasses shares some similarities but may have differences in the techniques, materials, and care required due to the specific properties of each frame material.
2. How to Ensure Quality Control When Sunglasses are Made
The frame is a crucial component of eyewear, as it not only holds the lenses but also directly touches the wearer’s face. It is as important as food safety. Therefore, quality control is vital in the production process of eyewear frames. The following will outline key points and procedures for quality control in frame manufacturing to ensure the production of high-quality and reliable eyewear products.
2.1 Key points of quality control in the manufacture of glasses frames
2.1.1 Material Choosing and Checking Before Eyewear Making
Choosing high-quality materials is the first important step in manufacturing high-quality glasses frames. Different materials such as metal alloys, acetate cellulose, and others have unique traits and advantages. During the material check step, it is important to ensure that the materials meet the design needs and test for appearance, strength, durability, and more.
2.1.2 Manufacturing process control
We must carefully control each step of the production process to make sure the methods we use are stable and can be repeated. Processes like injection molding, metal stamping, and acetate processing need to follow specific steps to ensure that the quality of the products remains the same.
2.1.3 Check of sizes and parts during glasses manufacturing
The size and fit of the frame and parts are crucial for comfort and clear vision. We need to measure the eye rim of the front, including lens openings, nose pad position, and temple length. It’s also important to check that the parts are of good quality and reliable.
2.1.4 Quality sampling during glasses production
Regularly sampling and checking products during sunglasses production to ensure they meet quality needs. By checking, we can find possible quality problems and take corrective steps to ensure stable and reliable product quality.
2.2 Quality Control Process for Glasses Frame Manufacturing
2.2.1 Raw material check before manufacturing
Strictly check the materials used in the eyewear frames, including sizes of appearance, quality, strength, and other needles, to ensure they meet standards and needs.
2.2.2 Glasses manufacturing process control
During the production of eyewear frames, strictly follow standard operating systems to ensure the accuracy and stability of each process. Record and monitor key parameters and quality control points in the manufacturing operations.
2.2.3 Product check for eyewear production
Thoroughly check the finished eyewear frames for their appearance, size, and functionality. Make sure the products are defect-free, meet design needs, and meet customer expectations.
2.2.4 Quality recording and traceability of eyewear manufacture
Create a complete quality record and traceability system to report production data, check results, and how quality issues are addressed for each batch. This helps with tracing and understanding the quality of the products when necessary.
2.2.5 Continuous improvement of the quality of eyewear manufactured
By listening to customer feedback and analyzing data, we can find problems, identify opportunities for improvement, and take necessary actions. Continuous improvement is crucial for maintaining high product quality.
In the process of how to manufacture sunglasses frames, quality control is an important link to ensure product quality and user happiness. By strictly controlling key points and implementing quality control processes, we are able to produce high-quality, reliable eyewear frame products that meet consumers’ needs and expectations for eyewear.
In a market where competition is growing, the quality of our products is essential for building trust and a good reputation. It also ensures our brand’s ongoing success. We will always prioritize quality and strive to improve, offering consumers a better experience with our eyeglass frames.
3. Summary of How Sunglasses Are Made
How are sunglasses made? Above, we have shared in detail from design to material choice to the manufacture of beautiful glasses.There are rich pictures and video explanations in the article, which can give you a deeper understanding of how sunglasses are manufactured and how we control quality during the manufacturing process.
But a lot of content involves knowledge in the professional field, which will be difficult for us to read for the first time, so please have to read it again. If you have any questions, you can contact us at any time, so that you can more comprehensively grasp how glasses are made of.